Mold filling occupies a significant position in the entire casting process. The two factors, which greatly impact the flow process, are fluidity and turbulence.
FluidityFluidity, a technological feature, reflects the ability of liquid metal to flow continuously even as it solidifies, via a given mold passage, filling it to reproduce the detailed design. It is expressed as solidified length of standard spiral casting. Fluidity is controlled by various factors listed below,
- i) Metallostatic pressure, expressed as ? g h where ? is metal density and h is height of liquid metal column above the filling point. Higher the metallostatic pressure higher is the velocity of molten metal, resulting in higher fluidity.
- ii) Viscosity is dependant of the metal family, composition and temperature.
- iii) Surface tension is expressed as þ g h= y / t, where ý is the surface tension and t is the thickness of the plate.
- iv) Heat diffusivity controls the transfer of heat from the mold causing the molten metal to cool quickly and stop flowing.
- v) Back Pressure - When the molten metal rises in the mold filling can be hindered due to the backpressure created by compressed air in the cavity thereby reducing the metallostatic pressure. Venting enables to regulate the backpressure.
- vi) Friction caused by rough surface of sand mold also hinders metal flow, hence a mold coating of water based silica flour and graphite is recommended to lower the friction and increase the fluidity.
Turbulence
It indicates irregular and fluctuating flow with disturbance caused when inertia forces are higher than the drag forces and when there are obstructions in the path of flow such as change in thickness or a sharp corner. Turbulence can be of two types, namely.
- i) Bulk turbulence - It is the ratio of inertia to viscous pressure in a fluid and is expressed by the equation Re = þ V d / µ. The flow is usually turbulent when Re is more than 2000.
- ii) Surface turbulence -It is the ratio of inertia to surface tension pressure in a fluid and is expressed by the equation We= þ V2 r / y. The flow is turbulent when We is more than 100.
Mold Filling Defects
The three types of defects usually encountered during the mold filling process are discussed below,
- i) Incomplete filling - It is generally caused due to poor fluidity of molten metal giving rise to cold shut or misrun. Cold shut occurs when streams of molten metal arising from opposite direction fail to fuse completely. Misrun occurs incase of incomplete filling of the mold cavity.
- ii) Solid inclusions : These are generally caused due to turbulence in the molten metal giving rise to sand or slag inclusions. Sand inclusions are caused by bulk turbulence in gating channels or mold cavity whereas slag inclusions are due to surface turbulence in the path of molten metal.
- iii) Gaseous Entrapments : These are caused due to entrapment of air and gas in the form of blowhole and gas porosity.
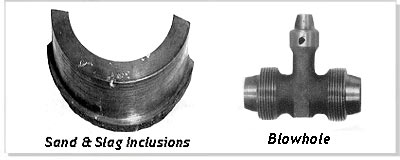
The process of flow of molten metal during casting is very transient involving major changes in the molten metal before it solidifies. The entire activity is broken in three phases i.e. gating channel filling, melt stream impinging on the mold wall and mold cavity filling.
In a scenario wherein the gating channels are perfectly designed the velocities in different sections are expressed as,
Vbasin2 = Vsprue1 = cf v (2 g (hpour + hbasin))
Vsprue2 = cf v (2 g (hpour + hbasin + hsprue))
Vingate = Vsprue2 Asprue2 / Aingate
= cf v (2 g (hpour + hcope)) Gsprue / Gingate
When the ingates are located at bottom or side of the casting the ingate velocity gradually decreases as the metal rises above the ingate levels. The instantaneous velocity in this case is expressed as,
Vingate = cf v (2 g (hpour + hcope - hi)) Gsprue / Gingate
Thus the filling time for the entire gating system is determined by ascertaining the velocity of molten metal at each stage such as basin, sprue, runners and ingates. It is also assumed that castings fills layer wise and the time Gating parameters for filling analysis to fill a layer is expressed as Gating parameters for filling analysis wherein Ai is the cross-sectional area being filled, ?h is the layer thickness; and Aingate-j and Vingate-j are the cross-sectional area and the instantaneous velocity respectively of ingate j. Further the total time can be calculated by adding the incremental time required for filling all the layers of the mold cavity. However this method does not account for other aspects of mold filling such as splashing, rejoining of streams etc and hence a numerical simulation method is used.
Numerical SimulationIt is based on three equations for mass, momentum and energy balance expressed in differential form called as Navier-Stokes equations. These equations, expressed in a differential form are referred to as Navier-Stokes equations, given below. The first one is for continuity, the next three for momentum along x, y and z directions, respectively, and the last for energy.
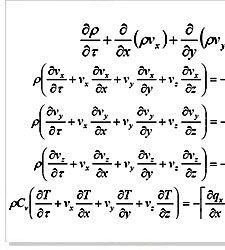
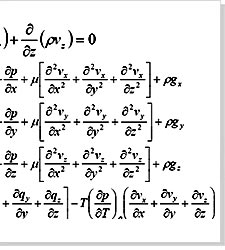
These equations can be solved using different methods like Marker and Cell, Simplified MAC, Solution Algorithm-Volume of Fluid (SOLAVOF). In all such methods the mold is divided into different cells classified as empty, full or surface cells, keeping a track of the location of the free surface.