The design of the feeding system should be such that the distinctive features that are desired in a casting are obtained. Specifically the defects related to solidification shrinkage should be avoided. Simultaneously the yield should be maximum and fettling problems should be minimum. Simple criteria can be used to assess the feeding design. All criteria are normalized and need maximization.
Internal Porosity :Within the decisive section of the casting the internal porosity’s size should not be greater than the acceptable size. The porosity could be macro porosity, which is greater than 1 mm size, or it could be micro porosity, which is in between 0.01 and 0.1 mm that could hardly be detected by the naked eye. Another term, which we can call mini-porosity, could be introduced to define intermediate sizes that are between 0.1 and 1mm.The criterion would be:

Here the porosity’s maximum size within the casting is given by maxi (di) and dmax denotes the maximum size that is allowed for the porosity (specification of the quality that the functional requirement determines).
Feeder Efficiency :The ratio between the amounts of feed metal that is required in Toto and the feeder’s total volume gives the efficiency of the feeder. The maximum efficiency that is possible for the feeder is compared with the feeder’s efficiency. The criterion could be given as:

In this equation, the casting volume is given by Vc, feeder volume is given by Vft and the volumetric shrinkage of the cast metal is denoted by a. The shape and the use of feed aids determine the maximum efficiency. The efficiency of open cylindrical feeders is low say smaller than 15%. But the efficiency can be increased 70% or above with the aid of an exothermic cover and sleeve.
Feeder yield :In order to get an increased yield the volume of the feeder has to be minimized. The criterion can be represented as:

In this equation the casting cavities per mold is given by Nc, volume of each cavity is given by Vc and Vft stands for the volume of the feeder i.
Fettling :At the time of fettling, care must be taken that the connection of feeder is quite small in comparison to the casting’s that portion which is connected. This is done so that the cracks and breakages are taken care of in casting at the time of fettling. In the presence of several feeders the criteria assessment value is determined by that feeder which is most probable to damage the casting.
Here for a feeder I the smallest dimension of the neck is given by tft, whereas the thickness of the connected portion is given by tci.
There could be defects related to solidification shrinkage in the casting due to poor design of the feeder system (feeders, feed aids, and necks). Macro, mini or micro porosity, shrinkage pipe (with extension in the casting), and surface links are included in this. Subsequent cooling of the casting can also cause defects like distortion and cracks. These defects are classified as external, internal, or sub surface according to their location. Let’s look at the most extensively used experimental techniques for feeding design validation.
Thermocouple Method :This method consists of embodiment of thermocouples at the strategic points in the mold. These strategic points are centre of thick sections, end sections, along the centre line of long thick sections and along the feeder axis. The temperature history of each thermocouple is recorded after the metal is poured into the mold. The solidification’s progress is given by the curves of time-temperature for varying locations within the casting. The choice of the thermocouples should be such that the heat absorption is minimum. The theoretical studies in the lab are best done using this method.
Non-destructive Testing :The methods of radio graphing (for the defects that are internal), and dye penetration (for the defects in sub-surface that have some openings leading to the surface), are used to inspect the casting. In addition to these, other methods that also exist are ultrasound and magnetic particle. These methods are more indirect and in order to interpret the readings more accurately a notable expertise is required.
Sectioning & Machining :As far as industrial castings are concerned this method is one of the most commonly used methods. Casting’s those regions that are suspected are made to go through the procedure of cutting through, polishing, and visual inspection. Feeder’s central planes along with their necks, casting’s those sections that are thick (for instance bosses), and the junctions between two or greater than two walls are used to obtain sections. The specified features are drilled and machined. Somehow the method is not reliable. It can falsely be assumed that the section, which is cut, is defect free, whereas a major porosity could be laying just a few mms away. Another problem with the method is that the surface, which is machined or drilled, may seem perfect but further machining may expose more porosity.
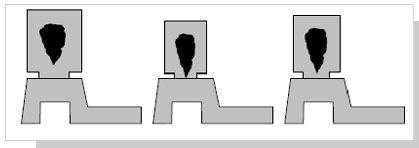
It can easily be inferred that the production castings that are free from defects cannot be guaranteed by sample castings’ experimental validation that is successful. The reason could be the design of the feeder being such that it allows for only borderline optimization. When no safety margins are left by the feeders (particularly where they and the castings connect with each other) to take care of variation of process parameters (like composition of metal and temperature of pouring). These surprises could be avoided during regular production if the feeding is slightly over-designed.