An alloy of tin, bismuth, lead and cadmium in the right proportions will melt well below the boiling point of water at just 70C. |
Tin is one of the earliest metals discovered by human being. Tin is known for a low-melting point (450°F) and its fluidity. It's very easy to form tin alloy with other metals because of its softness and formability. The metal has a high boiling point and is nontoxic and solderable. The difference of temperature between melting and boiling points, which is important for castings, is greater than all other metals.
Different casting methods used for tin alloy casting are gravity die casting, pressure die casting, and centrifugal casting. As there is little or no shrinkage occurs on solidification, components produced by tin-alloy castings are sound and dimensionally accurate. The design of molds should be such that sufficient amount of metal is fed to inside corners of the mold cavity. Carbon-steel or rubber molds can be used as tin alloys have low-melting points.
Property | Value and Units |
Atomic No | 50 |
Atomic mass | 118.69 amu |
Meltimg Point | 232 0C |
Boiling Point | 2625 0C |
Density | 7280 kg/m3 |
Electrical resistivity at 20 0C | 12.6µ
![]() |
Though, little bit expensive, tin is considered to be the perfect metal for casting. As the melting temperature is fairly low, simple molds, even molds made of special rubber can be used. Unlike lead, tin is non-toxic and it's shiny and doesn't tarnish.
Types and Features of Tin Alloys Pewter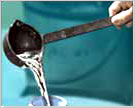
- It contain 1-8% antimony and 0.5- 3% copper.
- Excellent castability and workability.
- For spun pewter products, antimony content is usually below 7%, and pewter casting alloys contain 7.5% antimony and 0.5% copper.
- Due to its excellent drawing and spinning properties, wrought parts are usually made from pewter that is first cast into slabs, then rolled into sheet.
Bearing alloys
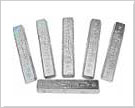
- Bearing alloys are low-friction materials.
- May hold high percentages of aluminum (to 80%), antimony (to 10%), or copper (to 10%).
- These alloys also contain babbitt metal, aluminum-tin, and bronze.
- Steel, cast iron, or bronze backing materials are used to strengthen its low mechanical strength.
- Bearing alloys are corrosion resistant, soft and comfortable.
Bronzes
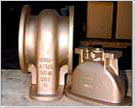
- Bronzes are alloys of copper and tin.
- Commercial grades usually contains 3-8% tin for wrought products and up to 12% for cast products.
- Gunmetals are bronzes, which also contain zinc.
Die-casting tin-based alloys
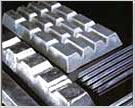
- The first materials to be die cast.
- Very low melting point and extreme fluidity of these alloys help castings inexpensively.
- It leaves little wear on molds.
- Main additions to tin in die-casting alloys are copper, Antimony, and lead.
- Mainly gravity or centrifugally die cast.
- Tolerances can be 0.0005 in./in., with wall thicknesses down to 1/32 in.
- Less or no shrinkage.
Fusible tin alloys
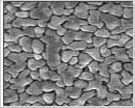
- It has low melting temperatures, usually below the solidus of eutectic-base tin-lead solders (361°F).
- Main alloying elements include bismuth, lead, cadmium, and indium.
- Generally, Fusible tin alloys provide electrical or mechanical links in safety devices.
- These alloys have applications in low-temperature solders, seals for glass and other heat-sensitive materials, foundry patterns, molds for low-volume production of plastic parts.
Tin and tin-alloy powders
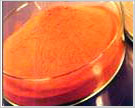
- Tin and tin-alloy powders are produced by atomization techniques.
- These powders are available in a number of mesh sizes.
- It has applications in the manufacture of powder-metallurgy parts, in the spray metalization of surfaces, and in tinning and solder pastes.