The protection of steel from corrosion by hot dip zinc galvanizing has been in practice for about 200 years, and the technique is still preferred for the long term protection of structural articles, which may be subjected to physical abuse during shipping and installation. This is generally due to the nature of the alloy coating developed when chemically clean steel is immersed in molten zinc.
In current use, galvanizing is typically referred to hot-dip galvanizing, which is a metallurgical process used to coat steel or iron with zinc. It is basically done to prevent corrosion of the ferrous item. While galvanizing is accomplished using non-electrochemical means, it serves as an electrochemical purpose.
Hot-dip galvanized steel is in effective use for more than 150 years. The importance of hot-dip galvanizing stems from the relative corrosion resistance of zinc that under most service conditions, is substantially better than steel and iron. In addition to developing a physical barrier against corrosion, zinc (applied as a hot-dip galvanized coating) cathodically protects the exposed steel. Moreover, galvanizing for protection of steel and iron is preferred because of its ease of application, low cost, and the extended maintenance-free service, which it provides.
Hot dip galvanizing deposits a thick robust layer, which may be more than essential for the protection of the underlying metal in some applications. This has found to be true in the case of automobile bodies, where additional rust proofing paint will be used. In such cases, a thinner form of galvanization is applied by electroplating, known as "electro galvanization". However, the protection that this process provides is insufficient for products, which are continuously exposed to corrosive materials, such as - salt water. Even so, most of the nails made today are electro-galvanized.
Galvanic protection can be attained by connecting zinc both electronically as well as ionically. In such a configuration, zinc is absorbed into the electrolyte in preference to the metal, which it protects, and maintains the structure of metal by inducing an electric current.
ProcessThe hot dip galvanizing process consists of following basic steps -
Oil and Grease RemovalIt is the first step, wherein a hot alkaline cleaner is used to remove dirt, grease, oil, and soluble markings. Also known as caustic cleaning, this process, however, do not remove paint, epoxies, and welding slag. These contaminants can be removed using sandblasting.
PicklingIn this step, a diluted solution of hot sulfuric acid is used to get rid of the surface rust and mill scale to furnish a chemically clean metallic surface, preparing the metal for the hot-dip process. This stage of galvanizing process can take anywhere from 30 minutes to 1-1/2 hours, which depends on the thickness or the complexity of the part.
FluxingIn the fluxing part of galvanizing process, the steel parts will pass through this flux (a zinc ammonium chloride solution) that floats on the top of zinc bath. Fluxing helps in removing oxides and is meant to prevent oxidation of the steel before it is coated with zinc. This flux is then pushed aside to make sure that the steel parts from the zinc path are removed cleanly.
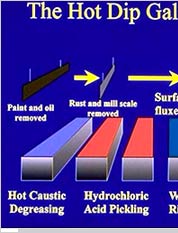
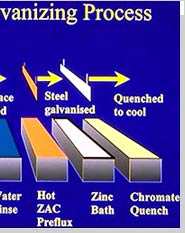
Galvanizing is the main stage, wherein the steel actually gets zinc coating. The steel is immersed into a bath of molten zinc that is heated between 820 - 850 F. During the process of galvanization, the steel comes up to the bath temperature and the zinc metallurgically bonds to the steel, thereby forming a series of highly abrasion-resistant zinc-iron alloy layers, topped by an impact resistant layer of pure zinc.
QuenchingIn this step, the galvanized steel is dipped into a dilute chromate solution to give a long lasting luster and to reduce temperature for prompt handling and inspection.
InspectionInspection is the final step in the galvanization process that is done to ensure compliance with the specifications. It is done to evaluate coating thickness, uniformity, adherence and appearance. Electronic testing gauzes are used to ensure quick, convenient and accurate measurements of the coating. In addition to this, some companies also issue certificates of compliance to ensure the proven quality standards.
Important Design FactorsUnderstanding the fundamentals of the important design factors for the galvanization of steel products help in getting the best protection for steel products. Hot dip galvanizing is a self inspecting process, which depends heavily on suitable design to attain a quality result. The primary difference between hot dip galvanizing and paint coatings is that the hot dip galvanized coatings can only be used on perfectly prepared surfaces. Some of the important design factors to be considered are -
- The zinc will not react with the steel to form the galvanized coating unless the steel surface is completely clean.
- The hot dip galvanized coating will not give results unless the zinc can closely contact the steel surface.
- The hot dip coating will not form unless the steel is heated to 4450 - 4600 C.
- Products cannot be galvanized unless they fit in the preparation tanks and galvanizing bath.
Design for Effective Galvanizing Falls into 4 Major Categories - Advantages
|
Advantages
Hot dip galvanizing offers several benefits and advantages to the specifier. Some of the important benefits include -
Corrosion Resistance
Galvanization coatings protect steel in three ways -
- Zinc weathers at a very slow rate and hence gives a long and predictable life.
- The coating corrodes preferentially to offer sacrificial protection to small regions of steel exposed through drilling, cutting or accidental damage.
- In the case, affected area is larger, sacrificial protection prevents sideways creep that can undermine coatings.
Coating Toughness
Galvanizing process is unique and produces coating that is metallurgically bonded to the steel.
Complete Coverage
All parts of the surface of metal - external, internal, awkward corners and areas with narrow gaps can be coated.
Speed of Application
Can be applied in minutes.
Lowest Lifetime Cost
Lower initial cost and long life makes galvanizing the most versatile, economic method of protecting metalwork.
Long Life
Galvanizing provides long life to the metal, which often exceeds 50 years.
Faster Construction
No site surface preparation is essential.