The design of tooling and process parameters determine the product design. The aim is to minimize rejections in the foundry, machining and during use. Cost of materials, tooling and manufacture, including energy and labor, comprise the total cost. For a process friendly design it is necessary that it is easy to manufacture, hastening development and have low tooling cost and energy requirement. Some guidelines to improve castability are given.
Part Complexity: a part with variations in width and holes etc is cheaper to produce by casting specially when product shape is simplified. This can be shown by three equations -
- The ratio of volume of the boundary to the volume of the part: V / (xyz), V being the volume of part and xyz its dimensions
- The ratio of area of a cube to area of part: 6(V)*2/3, A being the area
- The number of features:1/(1+N)*0.5 N being number of features
Parting line : The product must be designed using a particular draw direction, with minimum undercuts and aligning the sections to provide natural draft. Machined surfaces must be placed at the bottom of the casting.
Cored features - Internal features such as holes are produced by cores in a cast product. However cores add to the cost and may lead to defects while filling and solidification so their number must be reduced. Important factors are diameter, location in a thick section and distance from other holes and distance from edge.
Filling Characteristics : The part must be designed so that all sections are completely filled. There should not be sudden variations in thickness and sharp corners. Sections of different thickness may be connected with tapered sections. Long thin sections should be avoided as also those around which molten metal separate and again meets, especially if they are far from ingates, since this may cause a cold shut.
Solidification Characteristics : Two important considerations are fewer isolated hot spots and ensuring progressive solidification. Isolated hot spots can be found when regions of high mass are surrounded by lower mass. This may be due to higher volume or less area of heat transfer, example near a thin core in a thick section, radius of fillet being small at corner, cores being close to each other and ill-designed junctions (Fig 1).
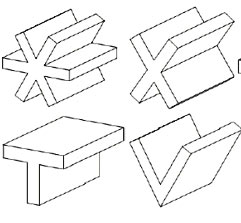
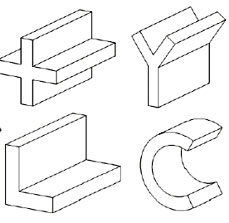
In a T-junction, the rib thickness must be half of the connected wall thickness and the fillet radius 0.3 times the wall thickness, while in a L junction this thickness must be 0.5 times (Figure 2).
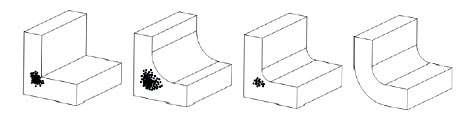
Progressive directional formation of solid is accomplished by varying section thickness gradually from end sections to densest, sections that harden last. The feeder should be able to be easily connected to the last solidifying section and there should not be any obstruction while filling. The feeder should preferably be connected to a flat surface. If there is a thin section in front it will solidify too early and feed metal will not be able to reach the hot spot.